Despite their popularity in Scandinavia and the fact they offer a number of benefits for home building projects, structural insulated panels (SIPs) have only recently been established as a mainstream option in the UK.
The system comprises pre-insulated panels, usually made from engineered wood-based sheets sandwiched together with a core of high quality rigid insulation – like polyurethane – in between.
A strong, lightweight system, SIPs can be manufactured to create large sections of wall, floor and roof, and are typically supplied in kit form to make a whole house.
“It’s a strange thing to say, but homes constructed with SIPs have a very solid quality to them, because you’re reducing the number of elements needed for a build,” says Malcolm Thomson, managing director of SIPs Scotland. “It makes a big difference to the overall feel of the property.”
The panels are made in a factory to your own bespoke requirements and then slotted together on site. Some prefab specialists can even supply them with windows and doors, plasterboard lining and service channels already installed.
This means that once the SIPs kit is delivered, the shell of your new home can be erected far quicker than with a traditional construction method. So, if you’ve made the choice to go down this route for your project, read on to find out how to make the most of this innovative system.
Superb energy efficiency
SIPs are renowned for offering exceptional thermal performance, which can significantly exceed Building Regulations without the need for excessively thick walls.
“They give you a very simple way to build to Passivhaus principles,” says Andy Clays, partner at SIPS@Clays. “You get a really well insulated property without making any extra effort, as there aren’t any gaps in the joins like you can sometimes find with other methods.”
While you can opt to install the panels on just the walls or the roof, for the best energy efficiency, Malcolm and Andy both recommend using a complete package.
“It depends on the desired performance that you’re trying to achieve,” says Malcolm, “but you’ll hit higher targets more easily with a full kit.”
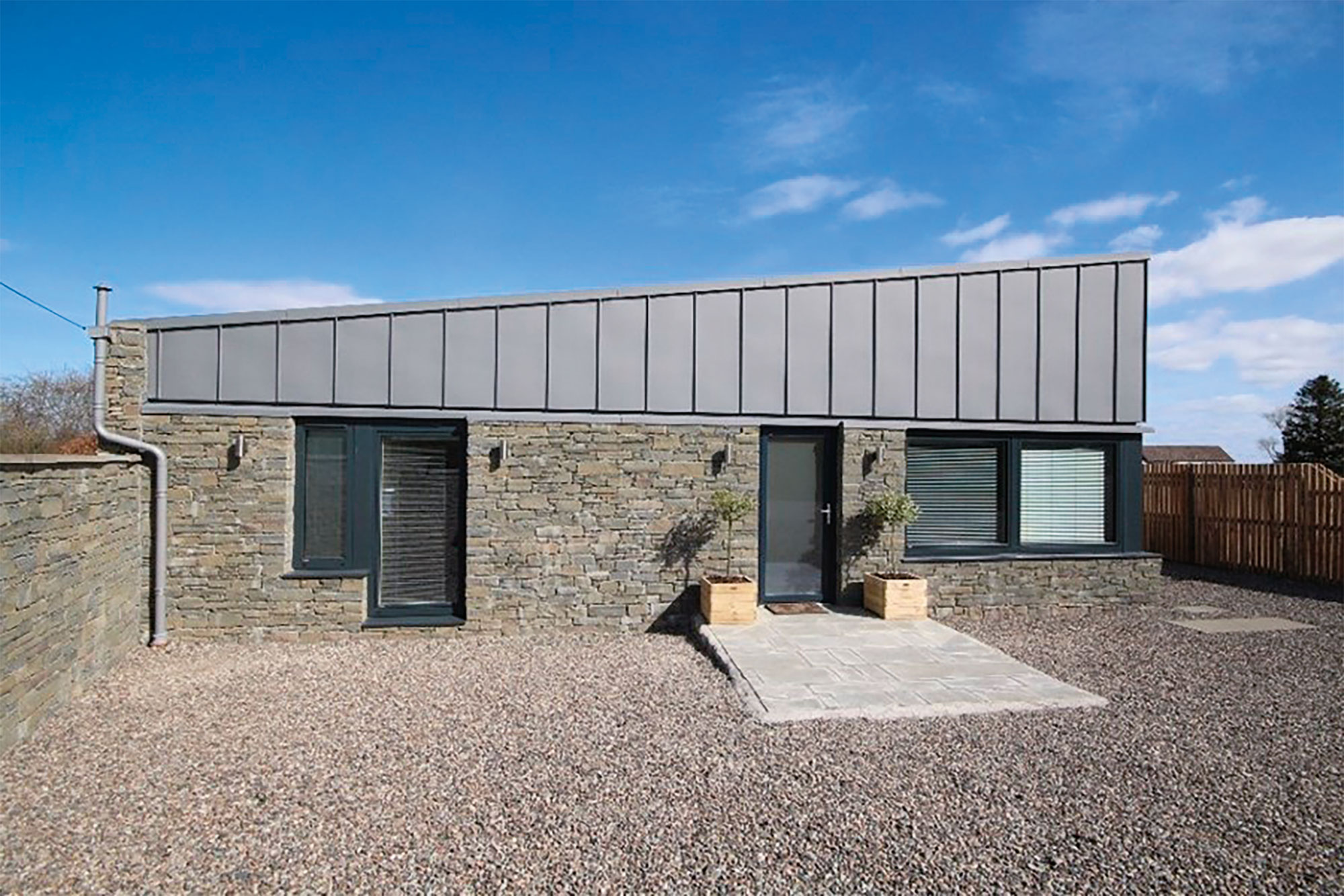
This contemporary home by SIPs Scotland features a traditional stone exterior topped with a sloping roof. The property was built with Kingspan TEK panels
That’s because working with a single system and supplier means the structural design, supply and erection is all done under one roof – giving you confidence the planned performance will be achieved.
It can also help with budgeting and project scheduling. “Because the panels are pre-insulated, once you’re on site and the house has been erected, the insulation is automatically done,” Malcolm continues. “With some other systems you have to go back and add in several extra layers. That takes a lot of time and labour and therefore can increase the subsequent costs.”
Design possibilities
When it comes to planning your SIPs home, arguably, the only potential limitation is your own imagination.
Houses of all sizes and shapes are possible, and after the structure is complete, it can be clad with pretty much anything you like. So, whether you want a traditional build with a classical stone finish or a modern white rendered abode featuring large swathes of glass, it is all very much achievable.
One design element that SIPs do lend themselves especially well to is creating spacious living areas in lofts, thanks to their strength and insulation performance in a relatively lean panel thickness.
“If you have paid good money for a plot of land, why would you put roof trusses in?” asks Andy. “You might be looking at what would traditionally be a two-storey residence with a standard covering, but using a SIPs system, you could achieve three full levels with a nice, versatile room in the attic.”
But while the sky is the limit when it comes to aesthetics, as with any build, you must hire the right professionals if you’re keen to get the best out of your scheme.
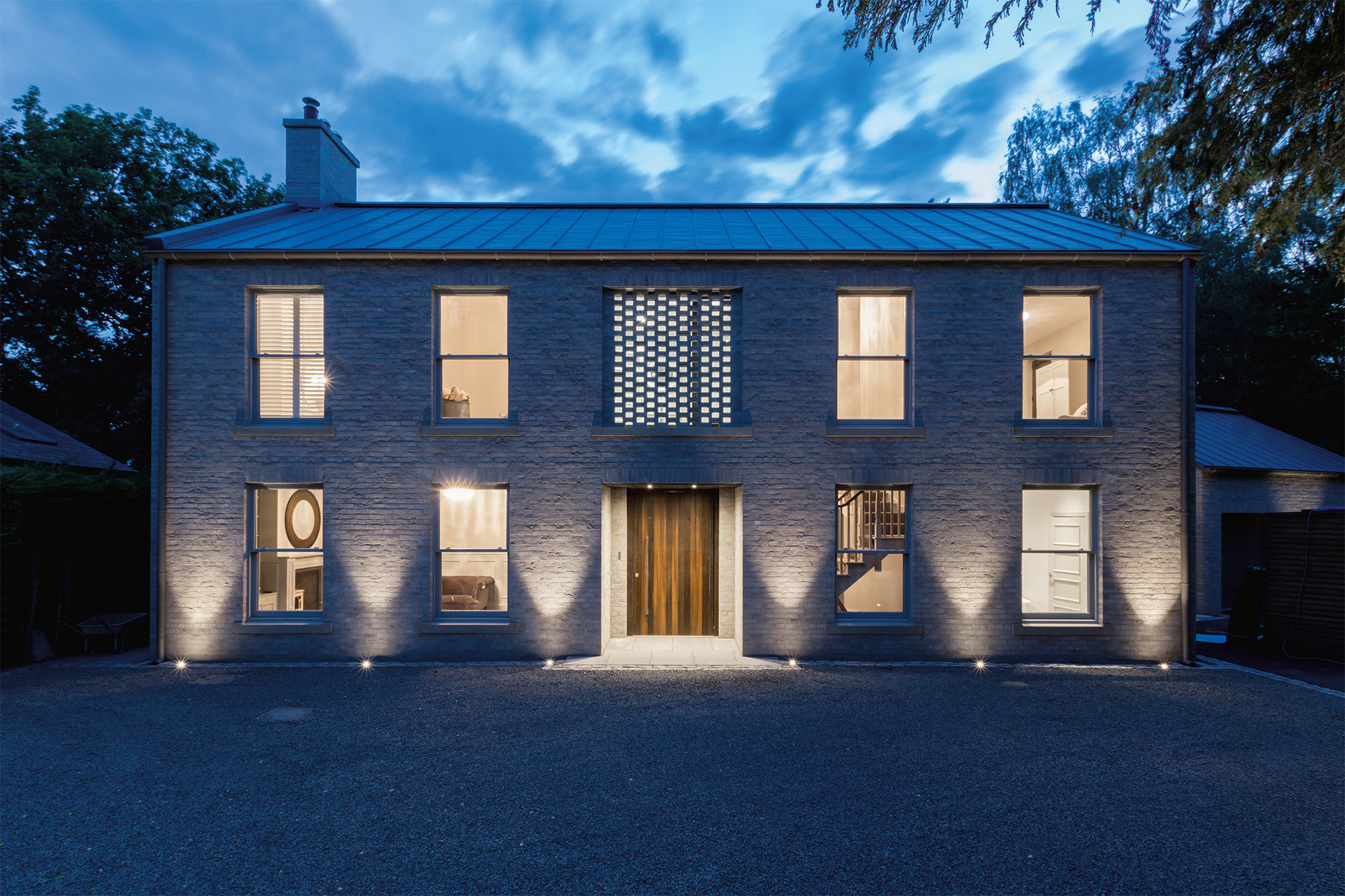
SIPS@Clays built this large, modern Northumberland home, which is clad in attractive grey bricks and features lots of fenestration
“Having a good architect with a strong knowledge of the system will assist in maximising the overall benefits,” says Malcolm. “They can help you with factors like window placement for solar gain and adding to the house’s overall performance.”
In terms of the SIPs structure itself, working with an experienced designer can help identify cost efficiencies. For instance, the most economical roof form will be to combine the panels with a ridge beam and apex gable ends.
“From a practical point of view, this is the most efficient way to build the kit,” Malcolm continues. “It’s very simple engineering-wise, which keeps fees low.”
As a result of the excellent levels of airtightness that are inherent with a SIPs build, you need to ensure that you’ve got a good stream of fresh air circulating throughout the house via proper ventilation.
“This is the same as it would be in any highly efficient property,” says Malcolm. He recommends installing a mechanical ventilation heat recovery (MVHR) system to maintain a fresh air supply.
Maximise glazing in your home
Opting for a high-performance setup such as SIPs can help to enable greater use of glass in your scheme.
The panels, the insulation and airtightness values can offset the comparatively lower U-values of windows, feature glazing and sliding doors.
Their strength and performance also means these panels can also be used to create wow-factor features like impressive vaulted ceilings.
There are limits to how far the SIPs can span without extra supports, of course, but your structural supplier can advise.
Should you decide to opt for a style with a lot of glass, Andy suggests adding more internal insulation to avoid any potential issues with cold bridges – especially if you’re aiming for Passivhaus or a similar standard.
“It’s a common sense approach that’s being more frequently implemented in the self build projects we see,” he says.
Attention to detail is vital here. “Many new houses are built with lots of glazing and the lintel heads around them can be quite substantial,” Andy continues.
“As there’s no insulation there, it becomes a weak point in your thermal envelope.” Adding 25 to 30mm of internal insulation to a standard 142mm panel can remove an element of
that cold bridge – allowing you to enjoy the aesthetics of contemporary design without increasing your heating bill.
Modern, light filled SIPs home for retirementWhen they decided to construct a home for their retirement, Brian and Donna wanted a quick and easy build. The speed of construction possible, thermal performance and airtightness of SIPs convinced them that it would be the best option. The panels and accompanying glulam beams also allowed them to have wide open spans and voids, which could have been more difficult to achieve with other materials. The couple’s architect son, Stefan, investigated several kinds of SIPs, including a local manufacturer, before settling on Kingspan TEK. “I had greater confidence in the product as it is from such a large, well-known company,” he says. He worked very closely with the supplier, Point 1 Building Systems, who provided their own engineering package for the structure. After an eight-week process, the panels arrived and were erected quickly in under three weeks. The one-and-a-half level design enabled the creation of double height spaces on the ground floor, with sloping ceilings and dormer windows to upper rooms. Externally, some of the SIPs panels were clad in a white through-coloured render and others with oak weatherboarding attached to timber battens, finished with several coats of lacquer. Aluminium-framed glazing was installed and the roof has been finished with interlocking slate-effect concrete tiles. Taking this approach to the covering has helped to keep costs down without impacting on the overall appearance of the striking modern property. |
Mix & match construction systems
One of the advantages of this system is that it can partner well with other construction methods. You could build in blockwork or insulating concrete formwork (ICF) for the walling, for instance, and top the house with SIPs to create a live-in loft.
The panels are also often used as an insulating wrap for oak frame builds. “You can keep the structural beams visible inside the house as a feature and wrap the SIPs around them externally,” says Malcolm.
“This gives you the energy efficiency of the structural insulated panels with the beautiful aesthetics of the oak internally.”
However, if you’re building to a strict time frame or want to minimise potential disconnects in the process, you might consider sticking to a singular system for all of the structural elements.
“Once multiple suppliers and trades start getting involved, there is a crossover of responsibility and accuracy,” says Andy.
“We often get asked to put our panels on the roof of a traditional construction. While this is perfectly doable, that house needs to have been built really precisely. SIPs are made to within 2mm of accuracy, so if measurements aren’t exactly right, it becomes tricky to determine who’s going to ensure everything fits together.”
Top image: SIPS@Clays created this sprawling modern build, which fully demonstrates the design potential of SIPs panels with its variety of jutting lines and angles
Find structural systems in Build It’s directoryAt the heart of any major self build or renovation project is the structural system you choose. Find specialist suppliers for brick-and-block, timber frame, structural insulated panels (SIPs), insulating concrete formwork (ICF) and alternative construction methods. |
The post How to get the best out of building with SIPs appeared first on Build It.
Article reference How to get the best out of building with SIPs
No comments:
Post a Comment