We’ve opted for a mix of timber cladding (we covered this in the September issue) and silicone render for the Education House’s external walls. They need to fulfil two key roles: prevent moisture ingress and provide an attractive finish.
Rendering involves fundamentally the same skillset as internal plastering – hence most plasterers do both types of work (and often floor screed, too). So, many self builders will engage the same team for these wet trade tasks.
In our case, however, we wanted to use a specialist to install the modern render we’ve selected. So alongside Drewett and Hunt’s plasterers, who are completing the internal tack and skim, we brought in silicone render specialist Prestige Energy, which has worked on a number of other projects at Graven Hill.
Benefits of silicone render
We’ve appointed K Rend as a partner to supply its silicone thin coat render, which has a fine textured finish, for the Build It Education House.
A cement-based system incorporating silicone, it offers a number of advantages over traditional solutions. Here are the key reasons we chose it:
1. It’s self-coloured Probably the biggest attraction of our silicone render is that the colour (there are 20 standard options) is embedded into the topcoat. So it doesn’t need painting, and there’s no redecoration to do over its lifetime.
2. It’s very flexible Properly applied and cared for, it has a long life expectancy of 30+ years. One reason for this is silicone render is more flexible than traditional products,
so it accommodates movement and resists cracking.
3. It’s water repellent The silicone imparts a hydrophobic quality, which means it’s highly water (and dirt) resistant. So much so, that this type of render offers an element of self cleaning – the only regular maintenance that might be required is a light pressure wash every few years.
There’s no doubt that silicone render is a premium product. Depending on your project, it might come in at double the cost of a traditional finish.
But the speed of application should reduce the amount of skilled labour required for installation, while its dirt-resisting qualities will keep a lid on long-term maintenance. So it can represent very good value for money for a self builder looking to stay in their home for many years.
K Rend sent out a sample pack for us to evaluate, which helped narrow down the options. We were confident a shade of white would be the right fit, as per Lapd Architects’ original design. But we couldn’t decide between two tones.
K Rend again stepped in to help, providing a couple of tubs for us to trial. That helped us settle on Limestone White, which will give a crisp, characterful finish to complement the larch cladding, yellow-grey window frames and red/brown roof tile blend.
Silicone render isn’t the only modern option on the market. A wide range of alternatives is available, each with its own benefits and considerations.
Applying the render
It’s best to have all the key elements of your home’s elevations done and dusted by the time the renderers get on site.
Ideally, the windows will be in, other external finishes (such as timber cladding) fitted, and the soffits and fascias installed. With those in place, getting a neat finish should be a doddle.
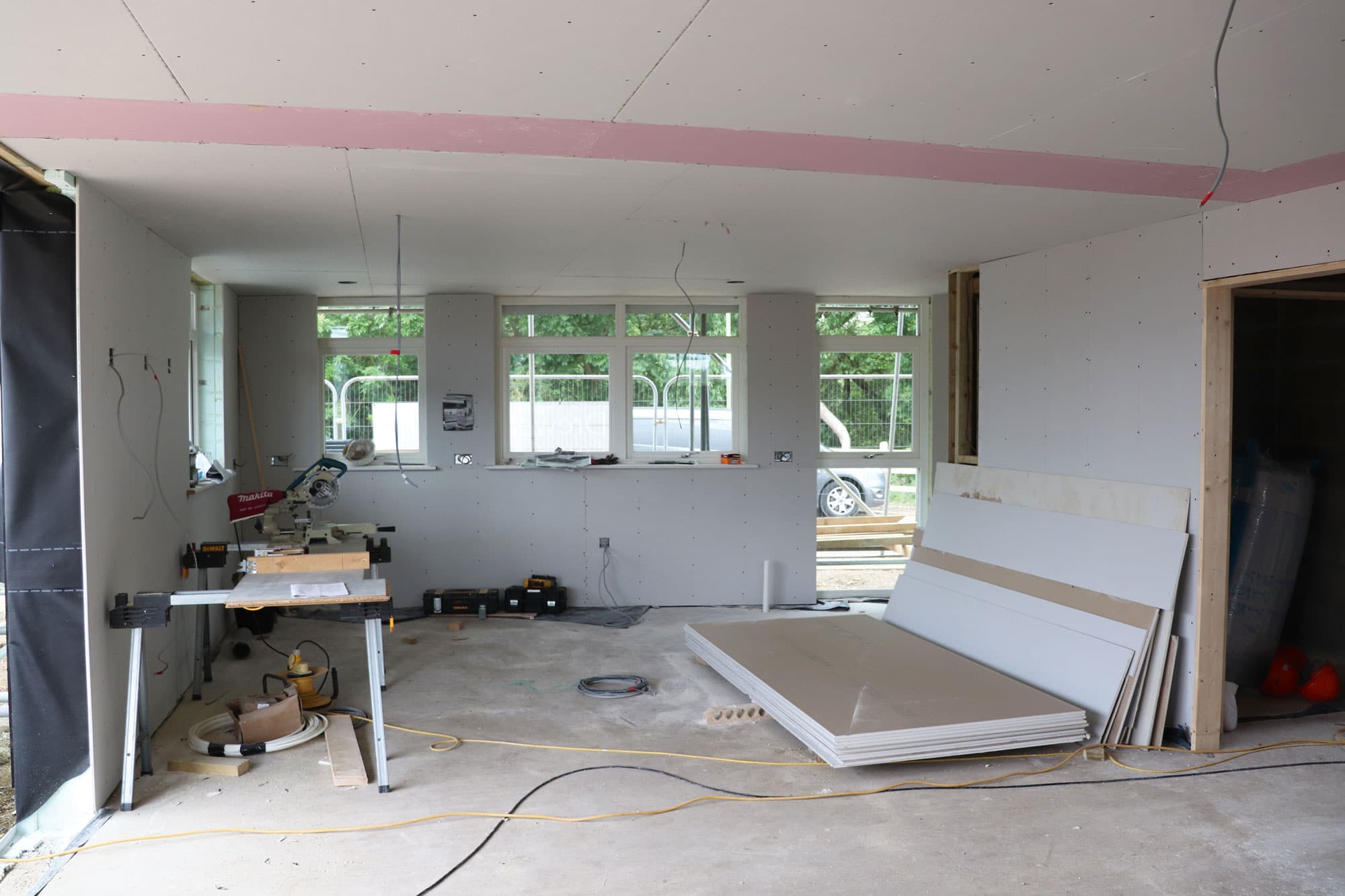
1. The ground floor part-way through tacking. The pink section in the ceiling is fire-rated plasterboard, which is required by Building Regs to protect structural steel
Prestige’s team, led by site foreman Darren, started by taping up the windows, doors and other joints with exterior finishes to protect them. Incidentally, because our timber windows have a microporous finish that needs to be allowed to breathe, they can only be covered for a short amount of time. All the more reason to use a quick-apply render solution!
With the prep done, the first step was to bed in the PVCu stop and angle beads where the render finishes or reaches internal/external corners (eg at the windows). This is the fiddliest bit of the job, and the team needed to build up a few corner beads to overcome thicker bits of silicone seal.
To keep up momentum, they set to work applying a base coat to the most straightforward elevations first. This was trowel-applied directly to the face of the insulating concrete formwork (ICF) walls, with an alkali-resistant fabric mesh embedded while the render was still wet. The mesh helps to smooth out any imperfections in the polystyrene, which reduces the risk of cracking even further and improves impact resistance.
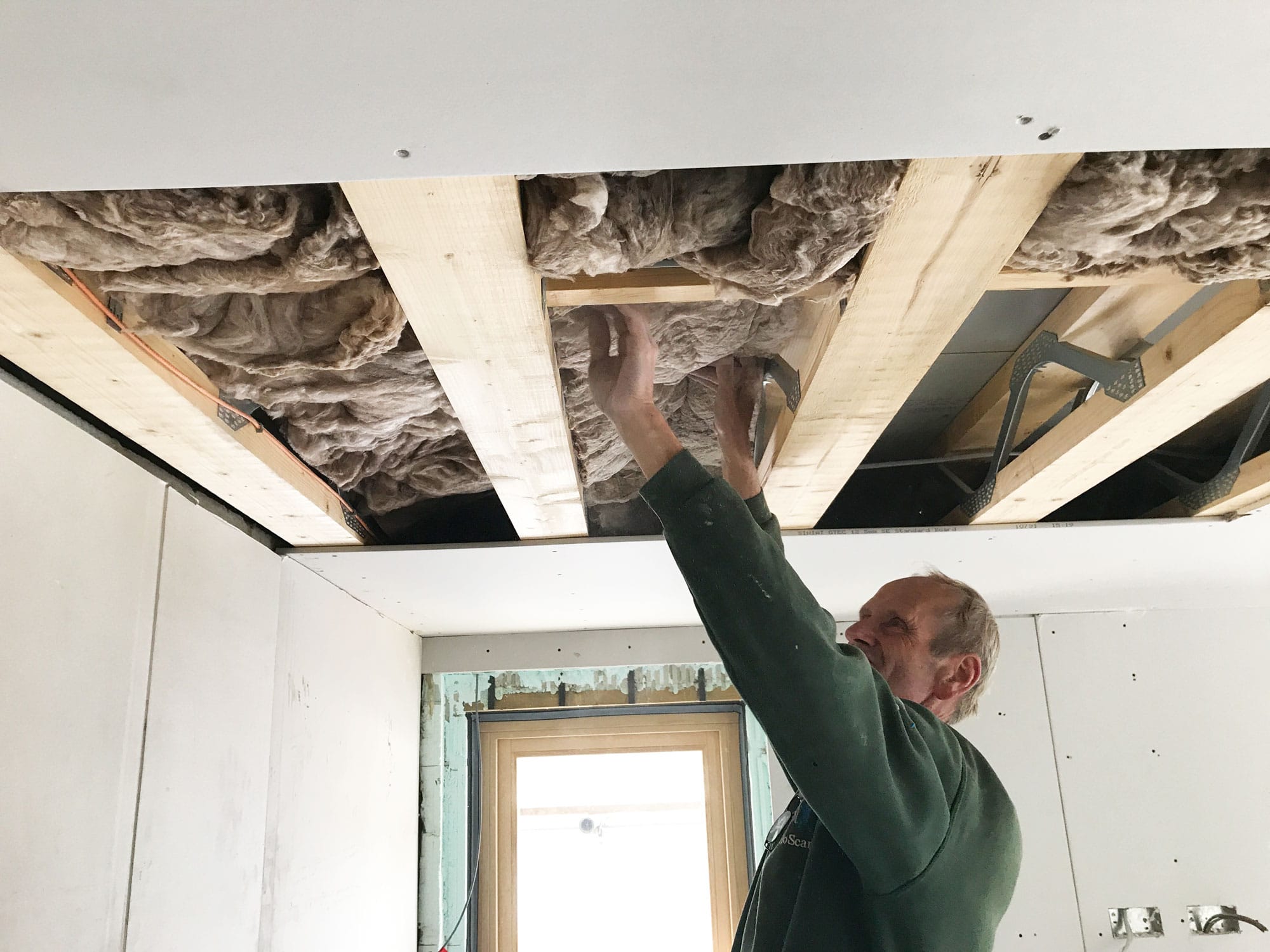
2. We’ve packed Earthwool acoustic insulation into the first floor ceilings and all the stud walls
Silicone renders can be spray-applied, but Prestige tell me this is more common on commercial projects rather than one-off houses. When the work’s on different elevations, it’s actually quicker and easier to trowel on: by the time you’ve set up the sprayer, you’d be half-way done anyway.
After 48 hours, the wall was ready for its next coat. Once that was cured, a primer was applied. To help streamline our build programme and enable us to get the scaffold down quicker, the team worked over a weekend to get this phase done.
Soon after, the walls were ready for the topcoat, which Prestige advised should be 1.5mm thick. This is enough to give a little bit of texture, while ensuring any imperfections in the substrate are completely hidden.
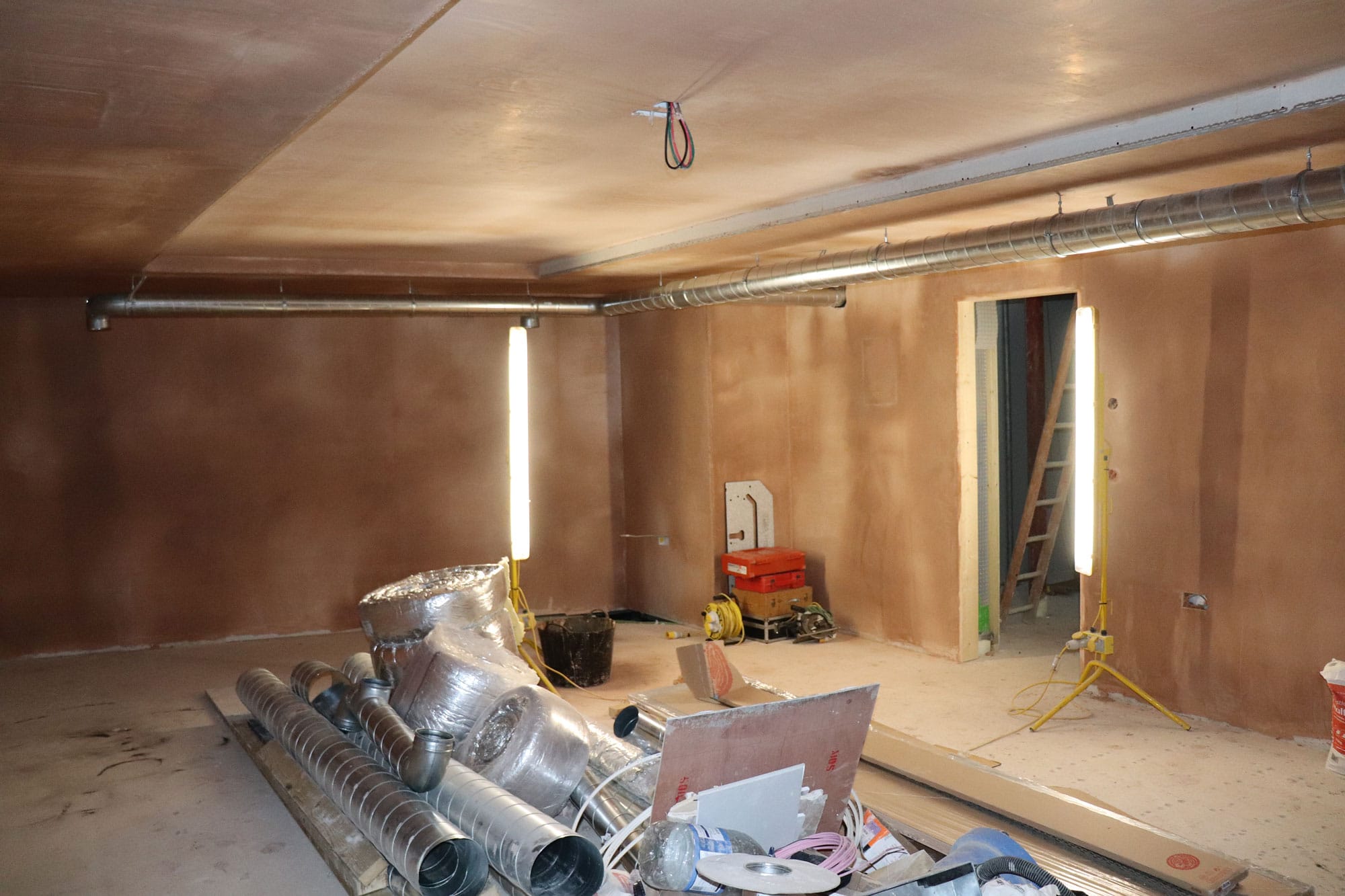
3. The main basement room, fully skimmed and complete with recessed ceiling
K Rend’s topcoats come in ready-to-go tubs with the colour already pre-mixed. The total build-up of silicone render is just 6mm-10mm, depending on how straight and plumb your walls are. That compares to around 25mm for a traditional cement render.
Add this up around the perimeter of a whole house, and this thinner finish can help maximise on precious internal space.
Internal walls & ceilings
Most self builders opt for plasterboard (sometimes known as drywall or tacking) and a skim plaster finish on the internal face of ICF walls. It’s quicker than traditional wet plastering, requires less skilled labour and avoids the usual 14-day drying time (a skim coat will dry in just two or three days).
As our Nudura system has fastening strips at 600mm centres, the boards can be screwed directly to the ICF wall (rather than battening out) to give a solid feel. The majority
of our service runs are located in the ceiling voids, with hot-knifed channels in the polystyrene walls down to sockets and switches. We can also plasterboard directly onto the SIPs panels in zones with vaulted ceilings.
In the basement, we’ve glued stud walls to the floor to avoid screwing into the waterproofing membrane. So we need to batten out the load bearing block internal wall in the vaulted hallway, to ensure the boards are flush all the way up. We’re also creating a recessed ceiling with LED lighting in the media zone, achieved using two different batten sizes.
Tacking
Plasterers are busy people, and ideally want to tackle projects in one big push so they can get the job done and move onto the next. On a gantt chart, you’d plan for them to come in once all first fix works are done so they’re basically the only trade working internally.
In practice, however, there are bound to be delays and overlaps somewhere (the eagle eyed among you will have noticed some images of tacked walls in last month’s update). It’s up to you, if you’re self-project managing, or your main contractor to try to minimise the impact of any setbacks.
One trick is to focus your resource on getting works done in sections to stay ahead of the game. Our tackers started in the basement and worked their way up – giving the rest of Drewett and Hunt’s team time to finalise prep on the storeys above.
Plasterboarding is quick work. For example, with the exception of a few areas of boxing out, the walls and ceilings in the main basement zone were tacked in a couple of days.
In most areas, we’ve used conventional 12.5mm-thick plasterboard, which comes in 1,200mm x 2,400mm sheets. Different thicknesses are available, which can be handy if you need to correct any discrepancies.
We’ve used SoundBloc acoustic board at the main bathroom to reduce noise transfer, but reverted to standard gypsum sheets with Earthwool insulation in the stud walls and ceiling voids. In some places, such as where there are structural steels, there’s pink-hued fire-rated plasterboard to meet Building Regulations.
The main area we couldn’t tack until later on in the build was the vaulted hallway. The crew needed an internal scaffold tower for access here, but erecting this too early would have blocked other trades, such as the floor tilers. So we made the decision to hold back on this section and concentrate on the rest of the house.
As we send the mag off to print, this area is mostly tacked and due to be finished imminently.
Skimming
With the boards in place, your other trades can crack on with any remaining first fix works – for example, the electricians will cut out for light fittings and install back boxes for switches and sockets.
Getting this work done before the plasterers return to do the skim will ensure best results – but some small post-plaster tweaks are inevitable. Skimming is done in two coats: the first gets the wall near-perfect, and the second thinner layer gives that ultra-smooth finish.
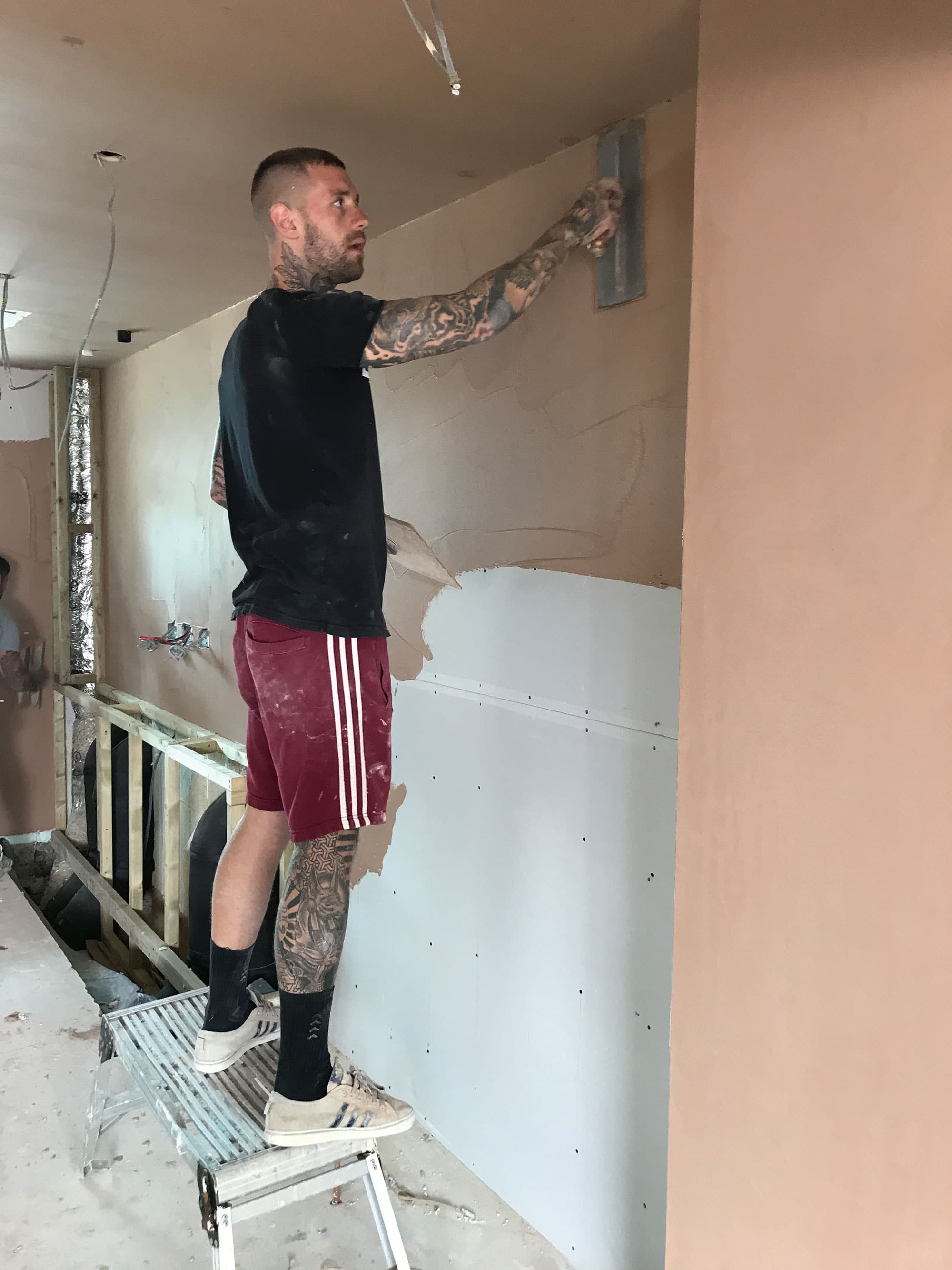
Skimming underway in the ground floor living room. It’s best to do the ceilings first to avoid disturbing the wall finishes with any muck that drops off the trowel. The final stages involve ‘troweling out’ the skim multiple times to achieve a really smooth surface.
The main prep is fitting beading at window reveals etc, and covering any joints with scrim (a special mesh tape helps to prevent cracking). After that, it’s all guns blazing. Drewett & Hunt’s plasterers brought in a big crew for this phase – and most of the ground floor was done in a single day.
That’s partly necessity: once you’ve started applying plaster to a wall, you have to complete it. Seeing the process in action is pretty impressive.
There’s an art to achieving perfectly smooth walls and ceilings ready for decoration – and it’s not something I’d fancy tackling DIY (get it wrong and you’d have to start all over again). But it’s bread and butter to skilled trades who know all the tricks and do it day-in, day-out.
The post Finishing the Walls and Rendering appeared first on Build It.
Article reference Finishing the Walls and Rendering
No comments:
Post a Comment